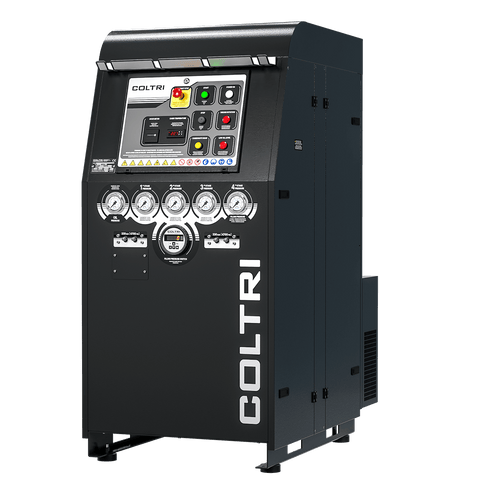
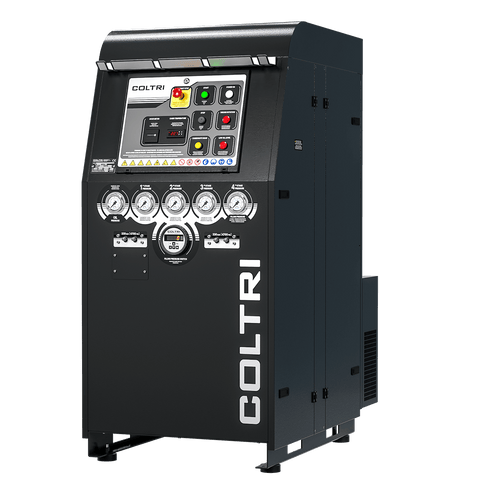
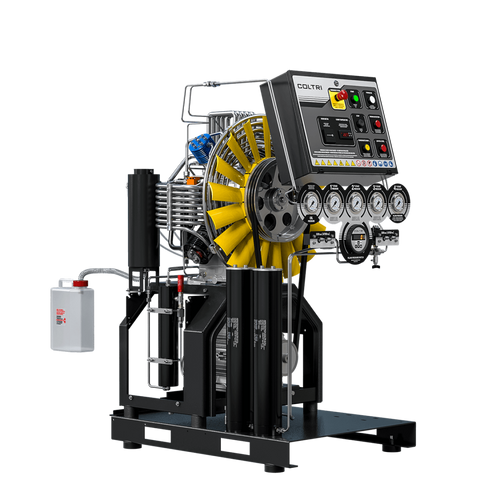

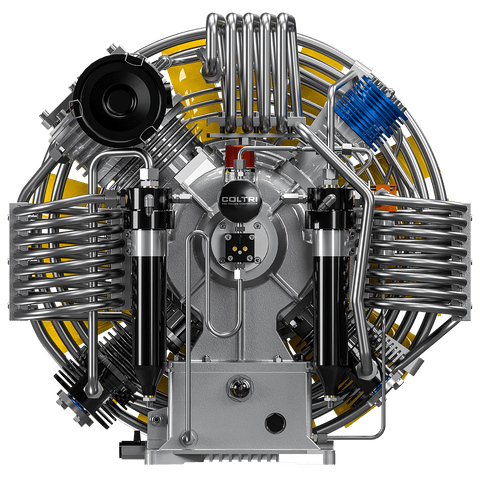
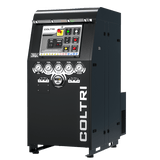
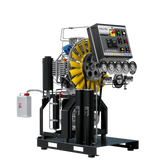
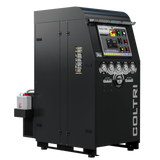
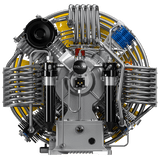
Coltri Silent HD
Call 605.543.5510 for questions and pricing.
4-stage high pressure pumping unit.
- Monobloc in aluminum,
- Crankshaft in forged steel
- forced lubrication on the 4th stage cylinder by gear pump
- Oil filtration
- Aluminum connecting rods
- Main roller bearings
- Roller connecting rod bearings
- 1st, 2nd and 3rd stage cylinders in special cast iron
- 4th stage cylinder in special treated steel.
- Stainless steel intake and exhaust valves
- Interstage cooling pipes in stainless steel
- Separator after the 2nd, 3rd and 4th stage
- Safety valves after each stage
- Oil level sensor
- Prepared for Hyperfilter filter system
Purification at the highest level.
Placed after the last compressor separator and before the pressure holding valve, the Hyperfilter purification system enables reliable treatment of the breathing air according to DIN EN 12021¹ when using original filter cartridges. The separator present between the 2nd and 3rd stage of the purification circuit allows to extract the greatest possible humidity. The filtering capacity with inlet air at 20 ° C and 200 bar is 4300 m³.
Electrical cabinet
- ON / OFF switch with motor protection switch.
- Digital electronic pressure switch that stops the compressor at the final pressure.
- Drainage of all separators between the individual stages and also of the final separator during compressor operation
- Timer for automatic condensate drain.
- Integrated no-load start (automatic drain every time the unit is switched off).
- 5 liter condensate collection tank, with silencer; capacity of about 3 liters, for the ecological disposal of condensate.
- Interstage pressure gauges display the working pressure for the individual compression stages. This pressure information allows you to check the tightness of the valves (inlet and outlet) of each stage and to quickly identify potential sources of failure.
Chassis
Silenced chassis with vertical development, made for environments that require a low level of noise. The oil level and drain reported outside, the control console equipped with inter-stage pressure gauges, the oil pressure gauge, the internal temperature indicator, the presence alarm and incorrect phase sequence, the lack alarm oil and the start, stop and manual condensate drain commands allow easy management and maintenance of the compressor.
Standard equipment
4 Filling connections of your choice of DIN 232, DIN 300 or INT/YOKE 232 bar
4 filling hoses of 1.2 m in length
Pressure maintenance valve
Interstage control gauges
Double PED certified Hyperfilter filter system
Cabin internal temperature with automatic switch-off
Automatic condensate drain
Automatic direction of rotation control
Electronic pressure switch with automatic shutdown
Oil level control with automatic shutdown
Oil pump
Automatic condensate drain with conveyor system in the tank
Frame color Black RAL 9005